MIT 2.007
Spring 2022, I took a class at MIT where students must individually design and fabricate robots for a competition at the end of the semester. I have learned a lot about open-ended design and how fabricating parts seems to always take significantly longer than expected. On the left is a simple robot I designed to test concepts. On the right is an early prototype of a lifting mechanism.


An important aspect of the class was taking a very open-ended objective of scoring points in a competition into specific design requirements. For instance, raising the beaver on the board gave 30 points while requiring 20N of force and 0.8m of extension. On the right is my prototype lifting mechanism lifting said beaver. All of the parts in the robot were designed and fabricated by myself using waterjet cutting, machining, and sheet metal bending.


Shown below is that same lifting mechanism in an early stage. It is controlled via PID using a potentiometer at the joint as an input. This design combines a rack and pinion system with longer "arm" segments for structure. The lifting mechanism has 4 degrees of freedom, but 3 are coupled in software due to geometry constraints.
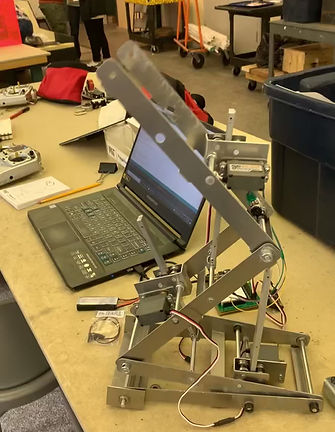

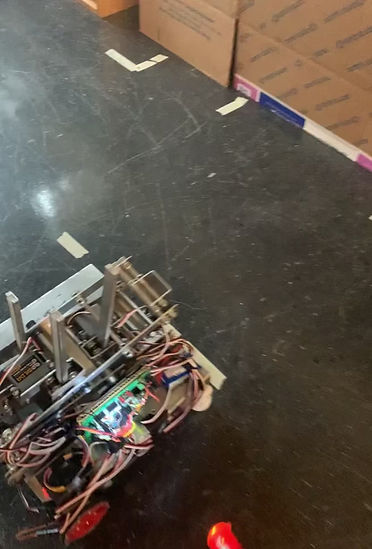
Testing the final product. Though my robot suffered crippling technical difficulties during the final competition, it still placed top 16. Overall, this project was an incredible learning experience.